
5125R UTILITY TRACTOR
Tractor
- Engine Power: 125 hp
- Easy to use transmission
- NEW integrated technologies (JDLink™, AutoTrac™)
- NEW optional suspended front axle
Apply For Financing
View Product Brochure
Features
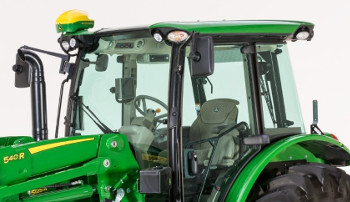
John Deere guidance systems offer many benefits to the operator, including optimizing machine efficiency, reducing operator fatigue, and the ability to work at faster speeds.
AutoTrac is an assisted automated steering system that automatically steers the machine through the field.
AutoTrac
AutoTrac is an automated steering system that can be operated from 0.5 km/h to 30 km/h (0.3 mph to 18.6 mph).
- Straight track: operate in absolutely straight lines by defining a point A at one end and a point B at the other end of the field. Skipping lines for easy and fast turns at the headland is possible.
- Curve track: the curve track functions are available on all AutoTrac tractor models. In particular, when driving the first passes at the headland, the system follows the shape of the fields curves, driving curves with a constant or increasing radius and using AutoTrac at the headland after completing the first row.
- Markers: when a tank is empty, for example, the system marks this point in the field. After having filled up the tank, the display will guide the operator to the location they marked.
- Turning view: on the headland, the operator must manually steer the tractor close to the next pass and then press the resume switch. There is no need to place the tractor exactly on top of the beginning of the next row. This means saving time on the headland.
- Shift track: this function allows the operator to return to the field to finish work they started yesterday. Satellites move the whole time the operator is away and so the guidance line is not at the place from yesterday. The operator can press one of the shift track buttons to fix the line for the day’s work.
Benefits:
- Reduced implement overlap
- Greater field working speeds
- Reduced fuel and input costs
- Optimized machine efficiency
- Reduced operator fatigue
The tractor controllers process differential global positioning system signals from the StarFire™ receiver, the wheel angle sensor, and a steering wheel position sensor. It uses these signals to steer the tractor via the electrohydraulic steering valve. The steering wheel position sensor detects slight motion of the steering wheel. If the operator performs manual steering or leaves the seat, the system is shut off. To activate AutoTrac, simply press the Auto Resume switch to engage automatic steering.
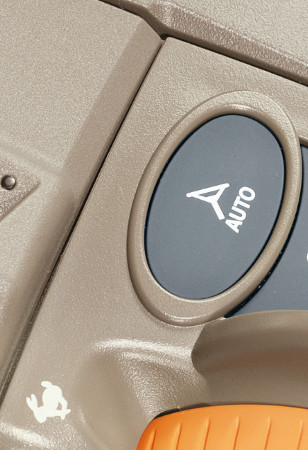
AutoTrac ready
The 5R Tractors can be equipped with an AutoTrac ready option from factory:
- GreenStar™/ISOBUS ready option
- Wheel angle sensor
- Electrohydraulic steering valve
- Steering wheel sensor
- Harnesses
AutoTrac Complete
AutoTrac Complete is a fully operational AutoTrac package ex-factory.
The 5R Tractors can be equipped with an AutoTrac Complete option from factory:
- AutoTrac ready (see AutroTrac ready section)
- Gen 4 4240 Universal Display
- StarFire 6000 Receiver
- Activation
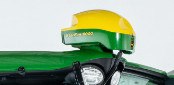

NOTE: For more information on additional displays, receivers, and Precision Ag Technology products, refer to Precision Ag Technology product information.
NOTE: To use AutoTrac, a GreenStar display and StarFire receiver is required.
Utility tractor users often work in challenging environments, including in and around barns, fields, or livestock areas. Maneuverability is a priority as space can be limited at times. Implementing the single-piece mid-frame designs and the structural oil pan enabled the wheelbase of the 5R to shrink by 100 mm (4 in.) when compared to the Final Tier 4 (FT4) 5M Tractors.
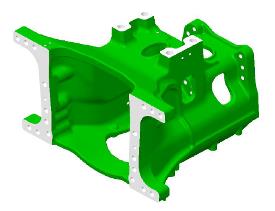
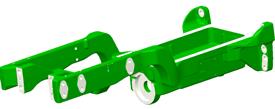
The shortened 2250-mm (88.6-in.) wheelbase provides best-in-class turning with a 12.1 turning radius without the use of turning brakes. This calculation uses 13.6R24 front tires, which provide 58 degrees of turning angle and a full 10 degrees of axle oscillation.
CommandQuad Manual transmission is base equipment on 5090R, 5100R, 5115R, and 5125R Tractors
The CommandQuad Manual transmission expands the proven reliability of the PowrReverser™ transmission with a 4-range, 4-speed transmission that enhances operator convenience and productivity through fully electronic manual range and gear shifting. The CommandQuad Manual uses the same final drives, rear axle, and differential as the already proven 5M PowrReverser transmissions. Rather than using mechanical synchronizers, the CommandQuad Manual utilizes powershift clutches. Also, electrohydraulic cylinders move the shift rails instead of a mechanical lever. This provides excellent ease of use and more efficient operation.
The CommandQuad Manual transmission is equipped with 16 forward and 16 reverse (16F/16R) speeds, a left-hand reverser, and four powershiftable gears in four fully synchronized ranges. The CommandQuad Manual transmission also comes with open centered hydraulics in base equipment, with the ability to option up to pressure and flow compensating (PFC) hydraulics from the factory. The base CommandQuad Manual transmission operates at speeds as slow as 1.9 kph (1.18 mph) with rolling circumference index (RCI) group 44 rear tires, and speeds up to 40 kph (25 mph).
For even slower speed options, a creeper is available as a factory-installed option (requires PFC hydraulics).
CommandQuad ground speed chart
CommandQuad with creeper ground speed chart
Operating the CommandQuad Manual transmission
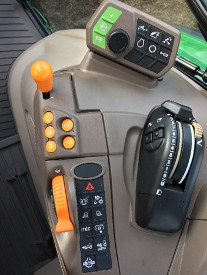
Range/gear controls
A single control lever, similar to the control used on the DirectDrive™ on 6R and CommandQuad™ on 7R, features an ergonomically designed and intuitive operator interface. This control lever provides manual gear and range change selection. This base transmission, although similar in operation to the optional Command8™ transmission, does not offer any automatic shifting capabilities.
Once the tractor is started, the operator selects a range by pressing one of the lettered range buttons on the right-hand console. The operator has five different selections to choose from - A, B, C, and two multi-range modes (BCD and CD). When a range with a single letter is selected, gear shifting is allowed within the specified range. When a range with multiple letters is selected, operators can shift between the designated ranges simply by using the toggle lever.
The gear within the range can be selected by using the transmission control toggle lever to electronically shift to a desired gear. After setting the desired throttle position, the operator can move the left-hand reverser to the forward or reverse position to start movement. The operator can shift up or down through the gears in the selected range(s) as needed.
The operator has the ability to shift through speeds and ranges without clutching by moving the toggle lever forward, toward the + indicator, or backward, toward the - indicator. A single movement of the toggle lever changes one gear at a time. Holding the toggle lever in either direction increases accelerates gear changes throughout the range at a faster pace.
When in a multi-range mode, a simple double toggle of the lever moves to the next range.
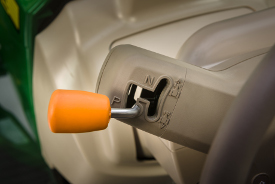
Left-hand reverser
The electronic left-hand reverser is standard with all CommandQuad Manual transmissions and provides neutral-to-gear modulation, which allows a quick, convenient, and smooth forward-reverse shuttle shifting at any speed. The shifter must be lifted from either park or neutral position to forward or reverse to activate. The parking brake is also electronically controlled through the left-hand reverser.
The left-hand reverser is a great feature for loader tractors. The operator's left hand can control easily tractor direction while the right hand manages the loader joystick and speed changes.
Standard advanced features of the CommandQuad Manual transmission
AutoClutch
With AutoClutch, which is standard on all 5R Utility Tractors, the operator no longer has to use the clutch to control braking and re-engagement of the tractor if so desired. The clutch pedal is still on the tractor for those operators that still prefer to manually foot clutch. This provides the ultimate in ease of use.
AutoClutch allows the operator to bring the tractor to a complete stop without clutching, while at the same time does not overload the engine. It also provides the ability to inch or creep the tractor forward or reverse on a level surface or incline. And it provides the ability to accelerate the vehicle back to normal speed when releasing the brake.
The operator can set the sensitivity setting of the AutoClutch system in the cornerpost display. There are three modes available:
- High sensitivity (default mode)
- Off – temporary setting only that is reset after a key cycle
- Low sensitivity
Low sensitivity would be typically used in transport applications with a towed implement. The low sensitivity ensures that the tractor and implement are stretched for better traction control.
Speed matching
When shifting ranges in a multi-range mode (BCD, CD), the transmission will shift to a gear that most closely matches the speed in the range from which the operator is shifting from, which improves operator comfort by making a smoother transition into a new range. There are two types of speed matching, passive and active.
With passive speed matching, when shifting to a new range, the tractor shifts to a selected fixed gear in the new range based on transmission ratios. For example, when shifting from C4 to D range, instead of shifting into D4 when the range is changed to D like a mechanically controlled transmission would do, the transmission shifts to a preset range and gear within range D. This most closely matches the transmission ratio from which the operator is coming from.
Active speed matching shifts up or down based on wheel speed during range shifts. This minimizes acceleration or deceleration when the clutch re-engages after a range shift and keeps a more consistent ground speed, improving operator comfort.
PowrReverser modulation
Similar to the 5M Utility Tractors, which offer a PowrReverser modulation dial to set aggressiveness of change in direction, all 5R Utility Tractors also offer PowrReverser modulation. Rather than a physical dial, the aggressiveness can be set through the cornerpost display. Settings can be set from 1 to 10, with 1 being the least aggressive direction change and 10 being the most aggressive direction change. A setting of 10 is popular for loader bucket applications where quicker directional changes are acceptable and more productivity is desired. Less aggressive modulation settings are ideal where smoother directional changes are required, such as bale stacking and pallet fork activities.
Start gear selection
Starting within gear 1 within every range has a negative impact on productivity. To minimize the amount of shifting required by the operator in many applications, start gears can be programmed by the operator when operating in any of the two multi-range modes.
In range CD, any start gear can be programmed into the cornerpost display between C1 and D1. In range BCD, any start gear can be programmed between B1 and D1. Let’s say that an operator programs B4 as the start gear for BCD range. Anytime the operator selects BCD mode by pressing that particular range button, the tractor will automatically begin in gear B4. The operator can of course shift to any range and gear between B1 and D4 from there, but the starting point will be what the operator has programmed. This results in less shifting and more productivity.
Within the fixed ranges (A, B, C), the preset start gears are A4, B4, and C4. These cannot be altered by the operator through the cornerpost display.
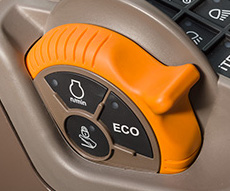
Foot pedal lock
Similar to cruise control in a car, the foot pedal lock allows the operator to set a constant speed using the foot pedal. The switch to engage foot pedal lock is also located on the right-hand throttle control. To operate the feature, the hand throttle must be on the low throttle position. Use the foot throttle to increase the tractor to the desired travel speed, and then press the button to engage the foot pedal lock. When releasing the foot throttle, the tractor will then maintain the speed selected. It can be disengaged by either tapping the brakes, or moving the left hand reverser control to neutral or park.
Independent programmable forward/reverse ratio
This feature is helpful in cyclical operations, such as loader work, where the operator wants to control the forward speed as a ratio of the reverse speed.
In manual mode, the tractor automatically selects a gear closest to the ratio desired by the operator. In auto mode, the tractor would adjust the set speed in the opposite direction. Ratios can be programmed up to 100 percent faster than the forward speed or up to 80 percent slower than the forward speed within the cornerpost display. This is adjustable in 20 percent increments (forward speed x 0.20, 0.40, 0.60, 0.80, 1.00, 1.20, 1.40, 1.60, 1.80, 2.00).
Another selection is independent; in this mode the tractor remembers the last forward and reverse gear setting. Once the gear is manually changed in the reverse direction, the gear will automatically go back to the last gear when changing directions. If the gear is not manually changed when in reverse direction, then the forward gear and reverse gear will remain the same when changing directions.
While the maximum forward ground speed is 40 km/h (25 mph), the maximum reverse speed is 30 km/h (18.6 mph).
Command8 transmission is optional on 5R Tractors
The Command8 transmission expands the proven reliability of the PowrReverser™ transmission with a 4-range, 8-speed transmission that enhances operator convenience and productivity through fully electronic range and gear shifting, as well as automatic shifting capabilities. The Command8 uses the same final drives, rear axle, and differential as the already proven 5M PowrReverser transmissions. Rather than using mechanical synchronizers, the Command8 utilizes powershift clutches. Also, electrohydraulic cylinders move the shift rails instead of a mechanical lever. This provides excellent ease of use and more efficient operation.
The Command8 transmission is equipped with 32 forward and 16 reverse (32F/16R) speeds, a left-hand reverser, and eight powershiftable gears in four fully synchronized ranges. The Command8 transmission also comes with pressure and flow compensating (PFC) hydraulics in base equipment. The Command8 operates at speeds as slow as 1.9 km/h (1.18 mph) with rolling circumference index (RCI) group 44 rear tires, and speeds up to 40 km/h (25 mph).
Operating the Command8 transmission
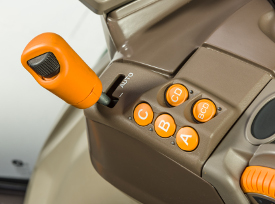
Range/gear controls
A single control lever, similar to the control used on the DirectDrive™ transmission on 6R and CommandQuad™ transmission on 7R, features an ergonomically designed and intuitive operator interface. This control lever provides manual gear and range change selection when in the left position, and auto selection when shifted to the right position. The thumbwheel is used to dial in the desired ground speed in the auto position.
Once the tractor is started, the operator selects a range by pressing one of the lettered range buttons on the right hand console. The operator has five different selections to choose from - A, B, C, and two multi-range modes (BCD and CD). When a range with a single letter is selected, gear shifting is allowed within the specified range. When a range with multiple letters is selected, operators can shift between the designated ranges simply by using the toggle lever.
The gear within the range can be selected by using the transmission control toggle lever to electronically shift to a desired gear. After setting the desired throttle position, the operator can move the left-hand reverser to the forward or reverse position to start movement. The operator can shift up or down through the gears in the selected range(s) as needed.
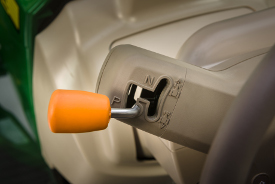
Left-hand reverse
The electronic left-hand reverser is standard with all Command8 transmissions and provides neutral-to-gear modulation, which allows a quick, convenient, and smooth forward-reverse shuttle shifting at any speed. The shifter must be lifted from either park or neutral position to forward or reverse to activate. The parking brake is also electronically controlled through the left-hand reverser.
The left-hand reverser is a great feature for loader tractors. The operator's left hand can control easily tractor direction while the right hand manages the loader joystick and speed changes.
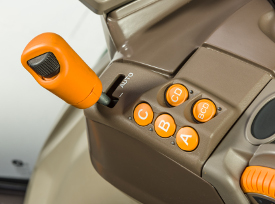
Manual mode
The Command8 features two different ways to operate transmission range and speed selections. In manual mode, the operator has the ability to shift through speeds and ranges without clutching by moving the toggle lever forward, toward the + indicator, or backward, toward the - indicator. A single movement of the toggle lever changes one gear at a time. Holding the toggle lever in either direction increases accelerates gear changes throughout the range at a faster pace.
When in a multi-range mode, a simple double toggle of the lever moves to the next range.
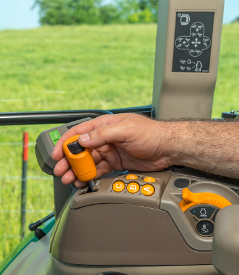
AUTO mode
Depending on load, auto mode will optimize both the engine and transmission by selecting the appropriate gear and rpm to optimize fuel efficiency. The only input needed from the operator is to set the target ground speed by using the thumbwheel. Once that target speed is set by the operator, the tractor takes care of maintaining that speed.
Once the operator has selected auto mode with the transmission shift lever, the following items will be displayed on the cornerpost display – auto activation, current ground speed, target ground speed, direction, range, and gear. If the operator has selected auto mode with the transmission control lever, then the operator can set the shift points of the transmission through the cornerpost display.
Features available in both manual and AUTO mode
AutoClutch system
With AutoClutch, which is standard on all 5R Utility Tractors, the operator no longer has to use the clutch to control braking and re-engagement of the tractor if so desired. The clutch pedal is still on the tractor for those operators that still prefer to manually foot clutch. This provides the ultimate in ease of use.
AutoClutch allows the operator to bring the tractor to a complete stop without clutching, while at the same time does not overload the engine. It also provides the ability to inch or creep the tractor forward or reverse on a level surface or incline. And it provides the ability to accelerate the vehicle back to normal speed when releasing the brake.
The operator can set the sensitivity setting of the AutoClutch system in the cornerpost display. There are three modes available:
- High sensitivity (default mode)
- Off – temporary setting only that is reset after a key cycle
- Low sensitivity
Low sensitivity would be typically used in transport applications with a towed implement. The low sensitivity ensures that the tractor and implement are stretched for better traction control.
Speed matching
When shifting ranges in a multi-range mode (BCD, CD), the transmission will shift to a gear that most closely matches the speed in the range from which the operator is shifting from, which improves operator comfort by making a smoother transition into a new range. There are two types of speed matching, passive and active.
With passive speed matching, when shifting to a new range, the tractor shifts to a selected fixed gear in the new range based on transmission ratios. For example, when shifting from C8 to D range, instead of shifting into D8 when the range is changed to D like a mechanically controlled transmission would do, the transmission shifts to a preset range and gear of D2. This most closely matches the transmission ratio from which the operator is coming from.
Active speed matching shifts up or down based on wheel speed during range shifts. This minimizes acceleration or deceleration when the clutch re-engages after a range shift and keeps a more consistent ground speed, improving operator comfort.
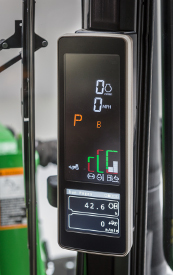
PowrReverser modulation
Similar to the 5M Utility Tractors, which offer a PowrReverser modulation dial to set aggressiveness of change in direction, all 5R Utility Tractors also offer PowrReverser modulation. Rather than a physical dial, the aggressiveness can be set through the cornerpost display. Settings can be set from 1 to 10, with 1 being the least aggressive direction change and 10 being the most aggressive direction change. A setting of 10 is popular for loader bucket applications where quicker directional changes are acceptable and more productivity is desired. Less aggressive modulation settings are ideal where smoother directional changes are required, such as bale stacking and pallet fork activities.
Start gear selection
Starting within gear 1 within every range has a negative impact on productivity. To minimize the amount of shifting required by the operator in many applications, start gears can be programmed by the operator when operating in any of the two multi-range modes.
In range CD, any start gear can be programmed into the cornerpost display between C1 and D1. In range BCD, any start gear can be programmed between B1 and D1. Let’s say that an operator programs B8 as the start gear for BCD range. This means that anytime the operator selects BCD mode by pressing that particular range button, the tractor will automatically begin in gear B8. The operator can of course shift to any range and gear between B1 and D8 from there, but the starting point will be what the operator has programmed. This results in less shifting and more productivity.
Within the fixed ranges (A, B, C), the preset start gears are A8, B8, and C4. These cannot be altered by the operator through the cornerpost display.
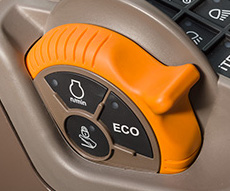
Foot pedal lock
Similar to cruise control in a car, the foot pedal lock allows the operator to set a constant speed using the foot pedal. The switch to engage foot pedal lock is also located on the right-hand throttle control. To operate the feature, the hand throttle must be on the low throttle position. Use the foot control to increase the tractor to the desired travel speed, and then press the button to engage the foot pedal lock. When releasing the foot throttle, the tractor will then maintain the speed selected. It can be disengaged by either tapping the brakes, or moving the left hand reverser control to neutral or park.
Independent programmable forward/reverse ratio
This feature is helpful in cyclical operations, such as loader work, where the operator wants to control the forward speed as a ratio of the reverse speed.
In manual mode, the tractor automatically selects a gear closest to the ratio desired by the operator. In auto mode, the tractor would adjust the set speed in the opposite direction. Ratios can be programmed up to 100 percent faster than the forward speed or up to 80 percent slower than the forward speed within the cornerpost display. This is adjustable in 20 percent increments (Forward speed x 0.20, 0.40, 0.60, 0.80, 1.00, 1.20, 1.40, 1.60, 1.80, 2.00).
Another selection is independent; in this mode the tractor remembers the last forward and reverse gear setting. Once the gear is manually changed in the reverse direction, the gear will automatically go back to the last gear when changing directions. If the gear is not manually changed when in reverse direction, then the forward gear and reverse gear will remain the same when changing directions.
While the maximum forward ground speed is 40 km/h (25 mph), the maximum reverse speed is 30 km/h (18.6 mph).
Features available in auto mode only (Efficiency Manager™ feature)
Efficiency Manager is automatically enabled when the shift lever is placed in the automatic mode gate. The set speed adjuster on the top of the single lever gear selector allows the operator to dial in the desired ground speed to establish a set speed for forward and reverse. Efficiency Manager allows the transmission to up- or down-shift and change engine rpm to maintain the set wheel speed. To reach the desired set speed, the throttle must be set to full engine rpm. This allows Efficiency Manager to shift the transmission and adjust engine speed to maintain the desired wheel speed.
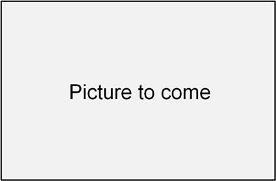
Eco on / Eco off
In some applications an operator may want to manage parameters for shifting points and minimum engine rpm. This can be accomplished with settings within the cornerpost display via Eco mode. Eco mode can be turned off and on with a switch located on the hand throttle. In many cases, operators will choose to utilize Eco mode in lower load conditions, such as transport. For tough field conditions, Eco mode is typically turned off. Minimum engine speed is adjustable between 900 and 2100 rpm.
Eco mode allows the operator to program two minimum engine speeds, one for when Eco is turned off, and one for when Eco is turned on. When Eco mode is activated, the transmission and engine will shift up and throttle back in order to try to maintain ground speed at the low engine rpm selected by the operator. For example, if a grower chooses a target speed of 12 km/h at an engine speed of 1200 rpm. The transmission and engine will work together to shift to higher gears and throttle back to find a gear that is able to get close to the 1200 rpm target.
When the grower gets to the field and wants to increase engine rpm to handle working tasks, simply turn Eco off with the Eco button on the throttle control, and the transmission and engine will then shift down and throttle up. The tractor will again target the speed selected via the thumbwheel, and the engine rpm that has been programmed into the cornerpost display for Eco off.
This is an excellent way to maximize fuel efficiency on a 5R Utility Tractor.
![Load control droop (power take-off [PTO] on) settings in cornerpost display](https://salesmanual.deere.com/sales/salesmanual/images/NA/tractors/pic_to_come.jpg)
Load control droop
Load control droop allows the operator to control the shift point of the tractor. The goal of auto mode is to prevent the engine pulling down below this preselected operating point by downshifting automatically. It commands an upshift so that the engine speed is above the load control set point (droop) with sufficient torque reserve. It also commands a downshift when the engine speed is pulled down below the load control set point (droop). The load control droop can be set within the cornerpost display in two modes, PTO on and PTO off.
The settings the operator can choose from in the cornerpost display are:
- PTO on
- High droop
- Medium droop
- Low droop
- PTO off
- High droop
- Medium droop
- Low droop
Selecting high droop minimizes shifting, while selecting low droop provides faster reaction to load.
Load anticipation
A load anticipation feature is standard equipment on all tractors equipped with a Command8 transmission. Its primary function is to increase productivity and provide more operator comfort by assisting the operator to handle expected high-load situations by automatically increasing the fuel economy optimal engine speed when working with implements. It can be used in both PTO and hitch activities, and can be turned on or off for each within the cornerpost display.
If turned on through the display, load anticipation is activated when:
- PTO turned on – engine speed automatically increases to the maximum engine speed
- Hitch movement – engine speed automatically increases to 1500 rpm when a hitch movement is detected
The load anticipation feature also activates when using PTO or hitch functions programmed within iTEC™ system sequences.
The premium cab is designed to provide superior visibility for the ultimate operating experience, especially in front loader applications. This cab includes all of the features of the standard cab operator station plus much more. Some of the key features include:
- Panoramic sunroof with sliding top shade and pull down front sunshade
- Factory-installed radio
- Bluetooth® system ready
- Satellite capable
- Deluxe sound system with front-corner-mounted speakers and subwoofer
- USB port (for sound only)
- Auxiliary cord connection
- Additional interior cab light
- Rear windshield wiper
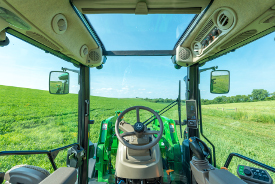
Visibility
Featuring a single-piece front windshield, forward facing visibility has improved by 7 percent for easier loader attachment hookups and easier following of rows in vegetable and other row-crop applications. Upward visibility has improved 80 percent with the panorama roof in the premium cab, providing for easier bale stacking, pallet stacking, and dumping loads into walled trailers.
For improved ease of use and visibility in both sunny and adverse weather conditions, the premium cab comes standard with several tools to help get the job done. To shield the operator from the sun on bright days, an easy-to-use sliding overhead sunshade with an integrated front pull-down shade is provided. To provide additional visibility in adverse conditions, such as rain or fog, the premium cab comes standard with a factory-installed rear window wiper, and exhaust vents built into the back of the front-mounted speakers.
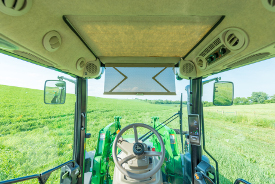
Sound and radio
Standard factory-installed radio is Bluetooth ready and has satellite capability. The premium cab also offers a deluxe sounds system with front-corner- mounted speakers and a subwoofer behind the seat for enhanced sound performance. The satellite radio capability feature makes it easy for operators to connect the sound system to SiriusXM® radio. The premium cab comes with a Bosch® deluxe radio, and offers both an auxiliary and a USB port to connect custom electronic devices. Using the Bluetooth feature, customers are able to connect to their phones to the radio providing wireless connectivity. Integrated into this deluxe sound system is an additional interior cab light in the bottom of the left-corner-mounted speaker.
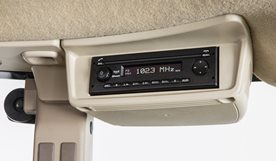
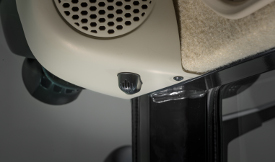
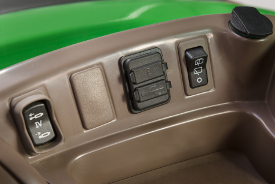
Bluetooth is a trademark of Bluetooth SIG Incorporated. Bosch is a trademark of Robert Bosch GmbH. Sirius XM is a trademark of Sirius XM Radio Inc.
Controlling speed and direction of the 5R Tractor in loader applications has never been easier. Whether the customer selects the CommandQuad™ Manual or Command8™ transmission, gear shifting and directional change is included as base equipment on any 5R Tractor that is equipped with mid selective control valves (SCVs). Both mechanical and electronic joystick options are mounted to the swivel seat. With a standard swivel seat, anytime the operator moves, the joystick also swivels along with it. This design improves operator comfort and operational efficiency by always having the loader controls at your fingertips.
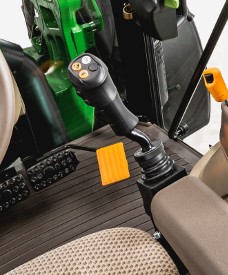
There are two types of loader joysticks available, mechanical and electrohydraulic. The mechanical loader joystick is mounted to the seat base, and is available with either open center or PFC hydraulics. The boom movement and implement rollback are controlled via cables from the loader joystick, which actuate the mid SCVs. If equipped with a third SCV for grapple functions, electronic buttons on the joystick control the opening and closing of the grapple.
On top of the loader joystick are buttons for gear selection. Pressing the rabbit or turtle buttons will shift the tractor by one gear. If the operator presses and holds the button, the tractor will more quickly accelerate through the gears when in a multi range selection (BCD or CD). Operating a loader tractor has never been easier.
The mechanical joystick can be easily locked out with a simple twist when the loader is not in use. Loader suspension can also be turned on and off on the face of the joystick with a switch.
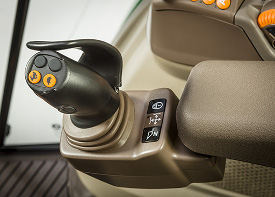
The electrohydraulic joystick is very similar to the mechanical joystick, but with a few key differences. This joystick also swivels with the seat, but is mounted at the end of the armrest rather than the seat base. Instead of cable control of the SCVs, it is fully electronic. The lockout is controlled electronically rather than with a mechanical lock. It is also available only with PFC hydraulics. The functionality is very similar to that of the mechanical joystick.
Either joystick option makes loader operation extremely comfortable on those long days of moving hay bales, stacking pallets, or general loader work.
**Electrohydraulic (EH) loader joystick is the only joystick compatible with CommandARM.
Loader joysticks with integrated reverser
Controlling direction on the 5R Tractor in loader applications has never been easier. Whether the customer selects the CommandQuad Manual or Command8 transmission, integrated joystick reverser is included as base equipment on any 5R Tractor that is equipped with mid selective control valves (SCVs).
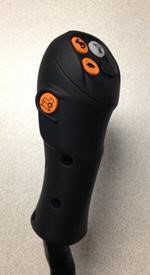
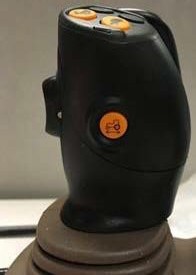
The two types of loader joysticks available, mechanical and electrohydraulic, are both equipped with the reverser functionality.
On the side of the loader joystick is a button for reverser function. By pressing the button, the tractor will change direction.
This joystick reverser feature makes loader operation extremely comfortable on those long days of moving hay bales, stacking pallets, or general loader work.
Take command of the 5R Tractor with the optional CommandARM console. Bring the functionality of selective control valves (SCVs), power take-off (PTO) engagement, hitch adjustment, and loader controls to one common place while still having the functionality to swivel the seat. Integrating large tractor technology into the 5R Series, operators will notice common features such as easily identifiable SCVs with color coding as well as the PTO engagement switch.
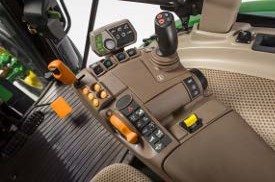
CommandARM provides individual access to the most frequently used controls.
- Engine throttle
- Transmission controls
- Electrohydraulic PTO
- Hitch/SCV controls (up to four rear SCV’s)
- Primary display unit (PDM)
- Loader joystick
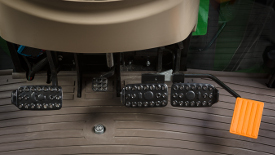
With AutoClutch, which is standard on all 5R Utility Tractors, the operator no longer has to use the clutch to control braking and re-engagement of the tractor if so desired. The clutch pedal is still on the tractor for those operators that still prefer to manually foot clutch. This provides the ultimate in ease of use, especially in applications where precise control and more stopping /starting is required.
AutoClutch allows the operator to bring the tractor to a complete stop without clutching, while at the same time does not overload the engine. It also provides the ability to inch or creep the tractor forward or reverse on a level surface or incline. Being able to inch or creep the tractor is an important tool for more efficient front and rear implement hookups. AutoClutch also provides the ability to accelerate the vehicle back to normal speed when releasing the brake.
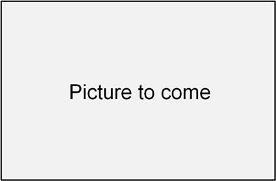
The operator can set the sensitivity setting of the AutoClutch system in the cornerpost display. There are three modes available:
- High sensitivity (default mode)
- Medium sensitivity
- Low sensitivity
- Off – temporary setting only that is reset after a key cycle
Low sensitivity would be typically used in transport applications with a towed implement. The low sensitivity ensures that the tractor and implement are stretched for better traction control.
The U.S. Environmental Protection Agency Agency (EPA) and Environment Canada requires all off-road diesel engines with 18.6 kW (25 hp) or more to meet stringent FT4 emissions regulations. John Deere uses the most efficient and cost-effective solution for the tractor package to meet emissions requirements at each horsepower level.
The engine powering the 5R is EPA certified Tier Level 4. This is achieved through a combination of a diesel oxidation catalyst (DOC) and selective catalytic reduction (SCR) using diesel exhaust fluid (DEF, or urea).
Several defining features on the 5R maximize the performance and reliability of the emissions package. A completely shielded DOC/SCR not only protects essential components from damage, it also keeps out dirt and debris. The well-packaged and tightly organized circulation system means there is more room to work around the tractor.
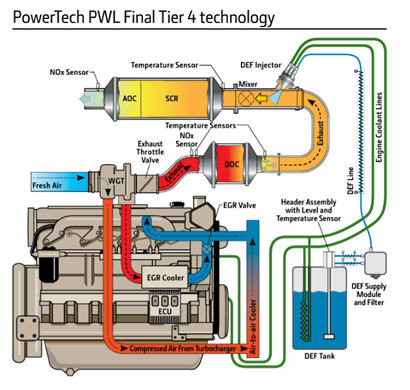
Key components of the emissions system include:
DOC
John Deere has chosen to utilize an DOC to reduce NOx to create less particulate matter. By no longer including a diesel particulate filter (DPF) and increased efficiencies in other areas of the tractor, the result is improved total fluid economy (diesel and DEF) and a lower cost to the producer.
The engine is programmed to aggressively respond to changes in power needs, which can temporarily increase particulate matter. Since the DOC removes particulate matter instead of the engine, the engine is left free to do what it is designed to do – deliver all of the power, torque, plus transient response needed.
DEF
DEF is an ISO 22241 standard aqueous urea solution consisting of 32.5 percent urea and has a freezing point of -11°C (12°F). A 11.4-L (3-gal.) heated DEF tank used in conjunction with a 143.8-L (38-gal.) fuel tank keeps the operator in the field longer. A DEF tank heater is integrated with a temperature sensor, and plumbed engine coolant lines are used to promote thawing and prevent freezing in the tank during cold operation.
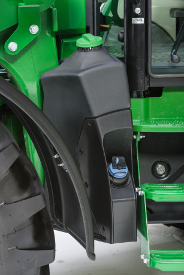
The electronic control unit (ECU) controlled supply module draws DEF from the storage tank 11.4 L (3-gal.) and provides a pressurized flow to the dosing module. When the ignition key is off, the supply module pump will reverse direction to return any accumulated fluid back to the tank. The supply module is also fitted with a replaceable filter to prevent contaminants from entering the dosing lines. Both the supply module and dosing lines are electrically heated and controlled by the ECU to determine when DEF dosing can begin.
The dosing module is cooled by engine coolant and used to inject DEF at a pressure of 130 psi (900 kPa, 9 bar) into the decomposition tube. A harness is connected to the dosing valve that relays the needed DEF to inject based upon the amount of NOx exiting the DOC measured from the NOx tube sensor.
The decomposition tube is the internal mixing device used to circulate DEF with engine exhaust prior to entering the SCR/AOC after-treatment device.
SCR
To reduce the NOx, DEF is injected into the exhaust stream. When the exhaust gases combine with the DEF in the SCR catalyst, the NOx is broken down into nitrogen and water vapor.
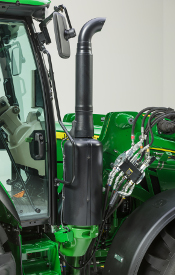
Exhaust gas recirculation (EGR)
EGR reduces the high temperatures where these compounds are formed in the engine cylinders by replacing excess oxygen with a prescribed amount of cooled exhaust gas.
Exhaust gases contain more carbon dioxide than oxygen. The EGR valve, in conjunction with the venturi tube, and engine control unit (ECU), allow a controlled amount of exhaust gas to enter the intake manifold to mix with the incoming fresh air.
Replacing excess oxygen with cooled exhaust gas leads to:
- Lower combustion temperatures, creating less NOx.
In addition, EGR allows for:
- Advanced timing
- Optimal engine performance
- Maximum fuel economy
For added performance and efficiency, the engine passes the exhaust gases through an EGR cooler before it enters the engine.
Exhaust airflow enters into the EGR cooler from the exhaust manifold near the turbocharger. Based on engine load, air temperatures, and rpm, the ECU opens or closes the EGR valve, allowing a measured percentage of exhaust gas to enter the intake manifold. The gases mix with the rest of the incoming air from the turbocharger and aftercooler before entering the cylinders.
Turbocharged engine
The PowerTech PWL 4.5L utilizes one turbocharger — a fixed geometry, wastegate turbocharger. Fresh air is first drawn into the low-pressure fixed geometry, wastegate turbocharger, and compressed to a higher pressure. The compressed air is then routed to the charge air cooler and then to the intake manifold.
Benefits of air-to-air aftercooling
- Lowers the intake manifold air temperature
- Provides more efficient cooling while reducing temperatures for greater engine reliability
- Higher volume of air flows into the cylinders
- Engine is capable of meeting the increasing horsepower demands
Combustion process with externally cooled EGR
Functions:
- According to engine operating conditions, the recirculated exhaust gases reduce the oxygen portion in the intake air to approximately 20 percent. Without any increase of the charge air pressure, the oxygen rate is not high enough to ensure a complete combustion of the fuel injected at high engine loads.
Advantages:
- Fuel-efficient combustion is achieved, because sufficient oxygen is provided.
A restrained, cooler combustion is realized, since the typical hot combustion process, which is generated by an oxygen surplus, is dampened by the inert exhaust gases. Hence, NOx emissions are reduced.
For more information regarding EPA regulations and the technology behind John Deere Integrated Emissions Control systems, please visit the following link:
https://www.deere.com/wps/dcom/en_US/campaigns/ag_turf/emissions/final_tier_4.page
Putting more power to the ground translates to increased productivity in demanding conditions. Simply put, torque is the useable power that can be achieved. More torque leads to more lugging ability which helps the operator be more productive.
5R Final Tier 4 (FT4) engines feature up to an 8 percent power bulge when put under load. The power bulge feature of the electronically controlled engine delivers additional horsepower as engine rpm drops below rated speed. Additionally, a 36 percent torque rise provides the force that maintains horsepower as engine rpm drops below rated speed.
When the tractor is under load, power bulge and torque rise work together to get through the tough spots and reduce the need to downshift. Horsepower and torque are mathematically related.
![]() |
As rpm drops, the only way to maintain or increase horsepower is to provide additional torque. The output horsepower is greater than or equal to rated horsepower as the engine is pulled down to 1750 rpm.
The peak torque rise also occurs near the rated economy power take-off (EPTO) speed for enhanced performance when operating in 540E power take-off (PTO).
NOTE: 5RH – 5115 hp only.
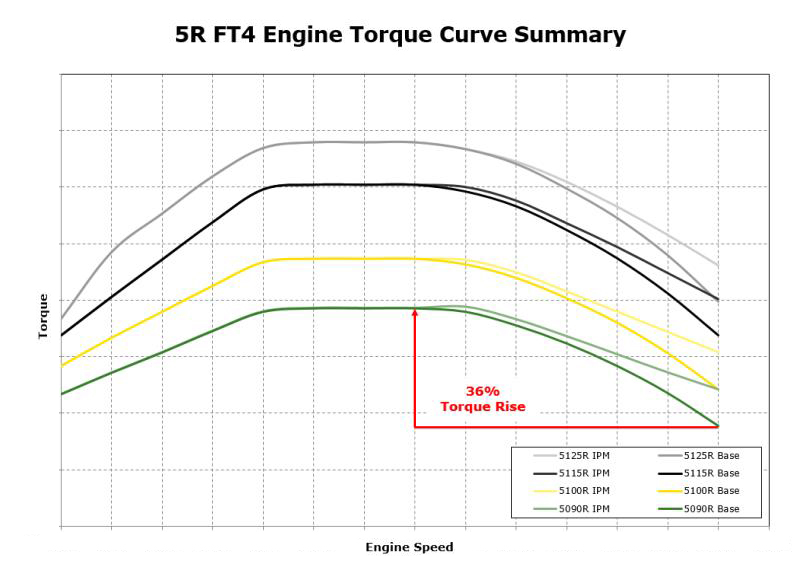
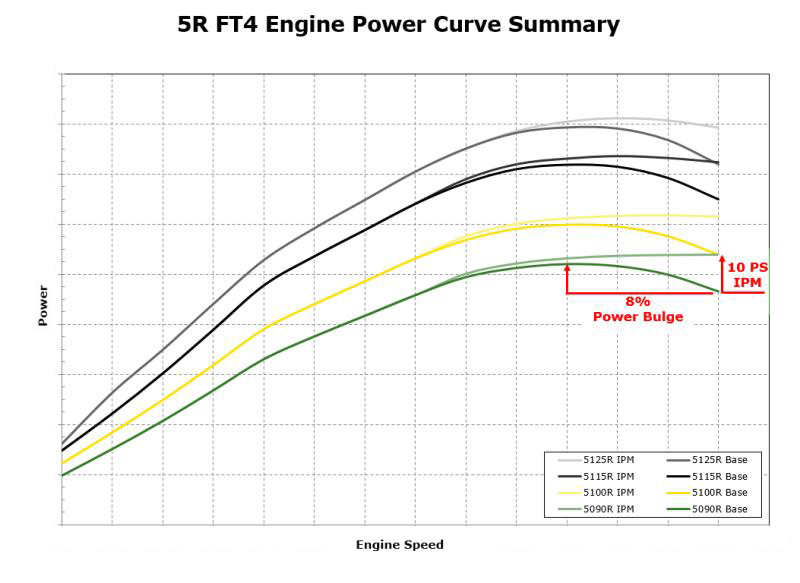
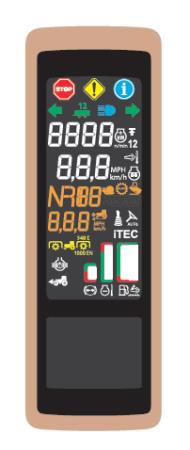
The digital cornerpost display features state-of-the-art electronic instrumentation and blends well with the narrow right-hand cab post. This intuitive design eliminates the instrument cluster once surrounding the steering column while increasing forward facing visibility. In addition to displaying machine information, the cornerpost display also serves as the primary interface between the tractor and operator when adjusting hitch, transmission, hydraulic, and engine settings.
Information included in the display:
- Stop, service, and information alerts
- Exhaust filter cleaning indicator
- Engine rpm (engine speed)
- Fuel-level gauge with low-fuel warning
- Diesel exhaust fluid (DEF) level indicator
- Engine temperature gauge
- Power take-off (PTO) engaged indicator
- Range information (F, N, R, P), transmission range and gear indicator
- Gear and AUTO mode indication
- Ground speed
- Target speed (in AUTO mode)
- Field cruise
- Differential lock indicator
- Mechanical front-wheel drive (MFWD) indicator
- Turn signal and hazard indicators
- High-beam indicators
- Start aid time remaining (with electric air intake heater)
- Creeper indication (if equipped)
- iTEC™ system indication (if equipped)
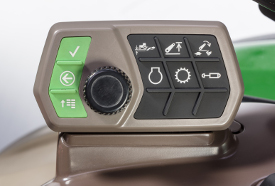
Interaction with the cornerpost display is primarily controlled with a button module mounted at the front of the right-hand upholstery. On the left side in green are a check mark button used to select items, a left arrow button that serves as a back button, and a menu button. The black wheel in the center is used for toggling within screens or adjusting settings.
To the right of the scroll wheel are hot buttons for frequently controlled settings, including draft control, hitch raise height, hitch drop rate, engine settings, transmission settings, and hydraulic settings. These buttons serve as shortcuts to make adjusting more common settings quicker and easier to access.
For operators wanting superior comfort and smoother driving, mechanical cab suspension is available for the 5R Series Tractors. The mechanical cab suspension reduces operator fatigue and improves comfort, especially when operating long hours in uneven fields. While offering a smoother ride, this factory-installed option also reduces noise and vibrations inside the cab from the engine, transmission, chassis, and implements one may be operating.
The cab rests on two rubber isolators at the front and two fully integrated shock absorbers at the rear which dampen the vibrations coming through the frame. The system provides stability to monitors in the cab helping to keep them in your viewing area.
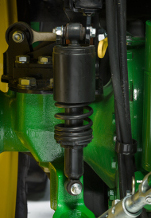
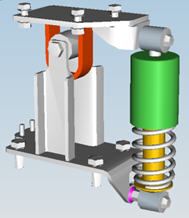
Specifications
Compare the specifications of up to 4 models
Key Specs | 5125r-utility-tractor Current Model |
---|---|
Engine description | John Deere 4045 PowerTech PWL |
Engine displacement | 4 cylinders: 4.5 L 276 cu in. |
Rated engine power | At 2200 per ISO 97/68/EC: 93.2 kW 125 engine hp |
Rated PTO power (hp SAE) | At 2200 per SAE: 83.5 kW 112 PTO hp |
Maximum PTO power | |
Transmission type | Standard: 16F/16R CommandQuad Manual Optional: 16F/16R Command Quad Manual with creeper 32F/16R Command8 |
Hydraulic pump rated output | Standard: 96.6 L/min 25.5 gpm Optional: 117.3 L/min 31 gpm |
Rear hitch category (SAE designation) | Category 2/1 |
Base machine weight | |
Maximum engine power | |
Engine specifications | |
Description | John Deere 4045 PowerTech PWL |
Engine type | |
Engine family | FJDXL04.5211 |
Rated speed | |
Aspiration | Turbocharged/Air-to-Air Aftercooled |
Cylinders liners | Wet sleeved |
Emission level | |
After treatment type | |
Displacement | 4 cylinders: 4.5 L 276 cu in. |
Engine performance | |
Rated power | At 2200 per ISO 97/68/EC: 93.2 kW 125 engine hp |
Rated PTO power (hp SAE) | At 2200 per SAE: 83.5 kW 112 PTO hp |
Maximum PTO power | |
Power boost | |
Engine peak torque | |
PTO torque rise | At 1600 rpm: 36 percent |
Intelligent Power Management (available in transport and/or mobile PTO applications) | |
Maximum engine power | |
Transmission | |
Type | Standard: 16F/16R CommandQuad Manual Optional: 16F/16R Command Quad Manual with creeper 32F/16R Command8 |
Reverser | Standard: Left hand, electrohydraulic Optional: Joystick reverser |
Clutch; wet/dry | Wet |
Creeper | 16F/16R CommandQuad Manual with creeper |
Hydraulic system | |
Type | Standard: Open Center Optional: Pressure-and-Flow Compensated (PFC) System |
Pump rated output | Standard: 96.6 L/min 25.5 gpm Optional: 117.3 L/min 31 gpm |
Available flow at a single rear SCV | Standard: 73 L/min 19.3 gpm Optional: 100 L/min 26.4 gpm |
Available flow at front SCVs | |
Number of rear selective control valves (SCVs) | |
Number of mid selective control valves (SCVs) | |
Number of front selective control valves (SCVs) | |
Joystick SCV control | Optional |
SCV control | |
Rear hitch | |
Hitch draft control load sense type | Electrohydraulic |
Remote control valves available | 2/up to 4 |
Hitch category (SAE designation) | Category 2/1 |
Maximum lift capacity behind lift points | Standard: 3038 kg 6700 lb Optional: 3564 kg 7860 lb |
Sensing type | Lower link |
Rear axle differential lock | |
Lift capacity at standard frame | |
Drawbar | |
Drawbar category | |
Maximum vertical load | |
Rear power take-off (PTO) | |
Type | Standard: 540/540E/1000 |
Engine rpm (at rated PTO speeds) | 540 at 2100 rpm 540E at 1645 rpm 1000 at 2103 rpm |
PTO actuation | Electrohydraulic |
Ground speed PTO option availability | |
Multispeed PTO option availability | |
Front hitch | |
Category | |
Electric power | |
Standard lift capacity | |
Front power take-off (PTO) | |
PTO speed | |
Rear axle | |
Type | |
Final drive type | Inboard planetary |
Differential controls | Electrohydraulic |
Axle type | Flanged |
Brakes, type and control | Hydraulic wet disc |
Rear differential lock | |
Load rating | |
Front axle | |
Type | |
Front axle differential lock | |
Load rating | |
Tires | |
Front | MFWD: 12.4R24 (320/85R24) R1W Radial |
Rear | MFWD: 18.4R30 R1W Radial |
Wheel tread range | MFWD: 2250 mm 88.6 in. |
Turning radius with brakes | MFWD: 3.37 m 11.1 ft |
Turning radius without brakes | MFWD: 3.7 m 12.1 ft |
Steering | |
Type | |
Electrical system | |
Alternator size | |
Battery options | |
Total cold cranking amps | |
Type of bulb in beacon (Halogen, Zenon, LED) | |
Type of bulb in headlight (Halogen, Zenon, LED) | |
Working lights | |
dB(A) rating for backup alarm | |
Operator station | |
Rollover protective structure, OOS | |
Seat | |
Cab suspension | |
Instructional seat | |
Display | |
Radio | |
Inner cab volume | |
dB(A) rating | 73 dBA |
Cab glass area | |
Front visibility | |
Safety glass rating | |
Dimensions | |
Wheelbase | MFWD: 2250 mm 88.6 in. |
Overall length | |
Drawbar clearance | |
Front axle center | |
Approximate shipping weight, Open;Cab | MFWD: 4450 kg 9811 lb |
Overall height | |
Weight | |
Base machine weight | |
Maximum ballast level | |
Maximum permissible weight | |
Capacities | |
Crankcase oil volume | |
Fuel tank | Standard: 144 L 38 U.S. gal. |
Diesel exhaust fluid (DEF) tank | |
Cooling system | |
Transmission-hydraulic system | |
Serviceability | |
Interval for engine oil change | |
Interval for hydraulic/transmission oil change | |
Interval for engine coolant change | |
Loaders | |
Loader | |
Lift capacity at full height | |
Maximum lift height | |
Precision AG | |
Guidance | |
Telematic | |
Remote diagnostics | |
Miscellaneous | |
Country of manufacture | Augusta, GA |
Side slope rating | |
Uphill/downhill slope rating | |
Tracks | |
Drive type | |
Midrollers | |
Track width | |
Tread spacing |
Reviews
1 reviews
- Filter
- Star Rating
- Value
- Quality
© 2025 Valley Plains Equipment LLC - Powered By