
C850 AIR CART
Air Cart
- 850-bushel (30-cu m) capacity
- 170 acres (69 ha) per fill
- Calibrate rate in half the time
Apply For Financing
View Product Brochure
Features
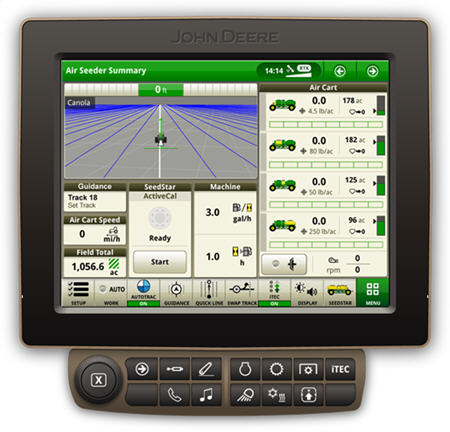
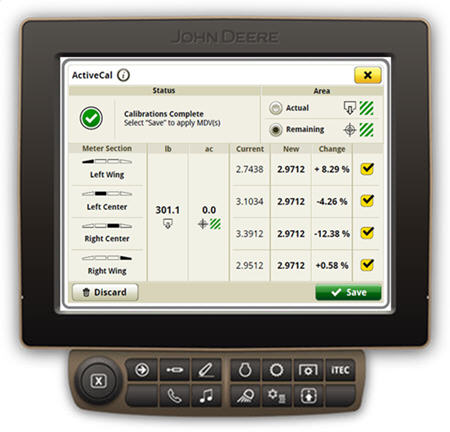
The more frequently calibration is completed, the more accurate a seeder will be. A number of variables, including product weight and changing climate conditions throughout the day, will have an effect on any volumetric metering system; with the John Deere ActiveCal system, calibration can be done from the cab of the tractor, while seeding, to minimize the variation in product metering.
The process to calibrate the implement starts with the Gen 4 4600 CommandCenter™ Display in the work setup page, where the operator defines product types, rates and selects meter rollers. Based on information entered into the work setup page, a preconfigured meter displacement value (MDV) will populate per meter. An initial manual calibration will give the most accurate MDV to start with. However, the preconfigured MDV will be a good starting point for growers who do not wish to manually calibrate.
The operator engages ActiveCal while stationary by selecting the button on the screen and then begins seeding. When enough product has been metered out, typically after about 8-12 acres, the Gen 4 CommandCenter will prompt the operator to stop when convenient to do so. At that time, the data points are calculated and a new MDV with percent difference is displayed on screen. The operator can accept or reject the new MDV. If accepted, the system automatically calibrates to the new MDV. If rejected, the system continues at the previously calibrated numbers.
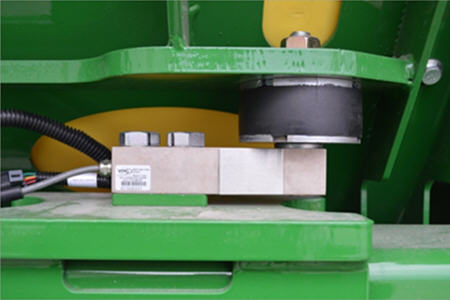
Monitoring the product levels in tanks has never been easier with the camera-ready feature of the 1910 and C850 Air Carts. The carts come pre-wired to accept a camera in each tank and on the rear of the machine. Cameras allow the operator to conveniently monitor product levels in each tank, which is especially reassuring when product levels are low. Cameras also provide the operator with visibility behind the cart when traveling down the road.
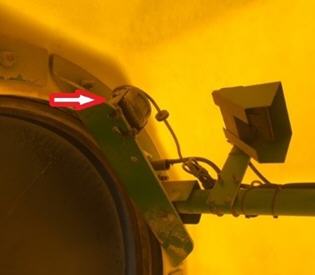
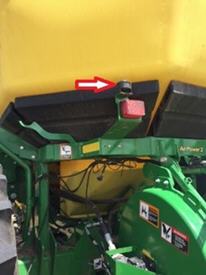
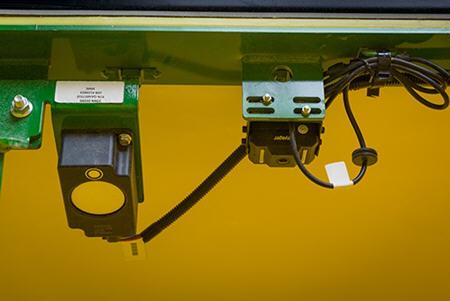
For the 1910 Air Carts, the producer has the choice of linking up to three cameras (CabCAM™ or Voyager® cameras) to a GreenStar™ 3 2630 Display or up to four Voyager cameras on a Generation 4 4600 CommandCenter™ Display or 4640 Universal Display. If the producer wants to view more than four cameras, a producer-purchased camera display will be needed.
For C850 Air Carts, the producer can use up to four Voyager cameras on a Generation 4 4600 CommandCenter Display or 4640 Universal Display. If the producer wants to view more than four cameras, a producer-purchased camera display will be needed.
NOTE: Generation 4 displays only support Voyager cameras.
While the 1910 and C850 Air Carts come pre-wired to adapt cameras, additional harnesses are necessary for connecting to the tractor, and a tool overlay harness will be needed for tow-behind carts. Please use the option codes below if ordering on a new machine or the part numbers for configuring an existing machine.
Option code | Description | Parts |
9610 | Tool overlay harness | AA94564 |
9615 | Gen 4 4600 CommandCenter Display tractor cab harness | AA93727 (order one per camera) AA94316 |
9620 | 4640 Universal Display tractor cab harness | SWTY268456 AA94316 |
9625 | GreenStar 3 2630 Display tractor cab harness | AA94319 AA94316 |
Some carts may require SWVOSCCAM and AA96311, a Voyager connector to CabCAM connector, on the rear of the cart.
CabCAM is a trademark of ATI Products, Inc. Voyager is a trademark of ASA Electronics, LLC.
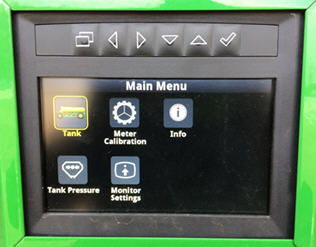
The durable display on the side of the cart will make filling and calibration easier than before. Selecting the menu button on the far left will take the grower to the main menu where they can select:
- Tank: shows product weight and tank fill level
- Meter calibration: preform a bag calibration without going back and forth to the cab to make inputs on the Gen 4 CommandCenter™ display
- Info: shows display and software information
- Tank pressure: shows the differential pressure between the tank and the meter for each individual tank
- Monitor settings: allows the customer to adjust the brightness of the display
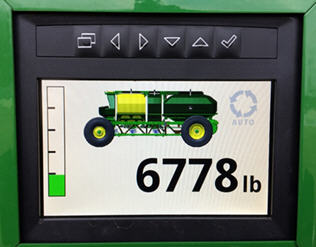
Tank weights and bin level will be shown on the first screen when the display is powered on. Navigating from one tank weight to another will be done by pressing the left and right arrow buttons.
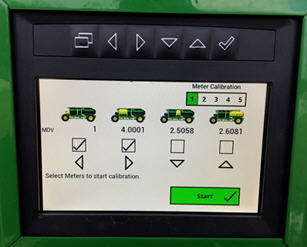
Meter calibration can be done cart side. To select the tank or tanks that need to be calibrated, press the display button that matches the icon below the respective tank on the screen.
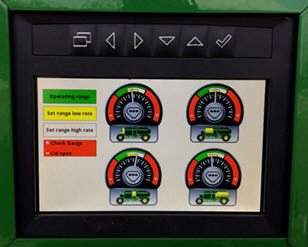
The digital screen replaces the mechanical tank pressure gauges on previous carts.

The total capacity of the C850 is 29,953 L (850 bu), measured by conveying product into the tank. The front tank is dedicated for low rate applications and holds 1762 L (50 bu). The remaining three tanks in order of front to rear are 9162 L (260 bu), 4581 L (130 bu), and 14,448 L (410 bu).
John Deere air cart tanks are solid molded polymer, known for superior corrosion resistance compared to steel while providing semi translucency allowing for visual verification of product level in day-time operation. Each tank is mounted in a cradle frame to eliminate interference between each other. The polymer material does not require weldments like on steel tanks. Weldments on steel tanks are prone to failure over time as the metal is fatigued under stress.
The improved top bevel design on tanks allow for greater capacity and meets the 29,953-L (850-bu) capacity without the need for shoveling product into the corners while conveyor filling.
Each tank has a wide single opening, which means it is easy for access for the conveyor and entry to the tank. Inside each tank is a ladder for cleanout access. Ladders in the tanks have been designed so that material cannot build up on steps. Top rails have been capped and sloped to ensure product sheds from the surface. When cleaning out the cart, the tanks slope steeply at bottom for product to flow easily and each tank is accessible for fill and cleanout with the conveyor.
Tanks come equipped with digital pressure sensor, ultrasonic bin level sensing, and camera-ready harnesses mounted from the factory.
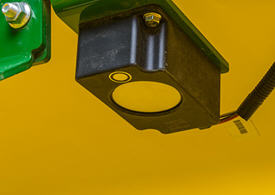
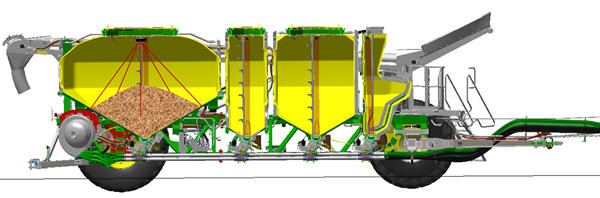
The John Deere ultrasonic bin level sensing system will increase the accuracy of bin level read outs in the cab and on the cart side display compared to the paddle design. The accuracy of this system is within 10 percent of actual product in the tank. Product in the tank is measured utilizing high-frequency sound waves (ultrasonic) that are emitted from the unit and received back when they reverberate off the product in the tank. These sound waves generate a digital signal which can be mapped across the angle of repose for the product in the tank. Using calculus volume can be determined from the convex slope determined from the ultrasonic frequencies. When metering two products into one airstream, ultrasonic is able to improve the accuracy of detection up to 50 percent more than traditional paddle sensors.
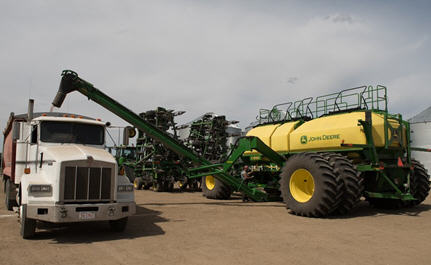
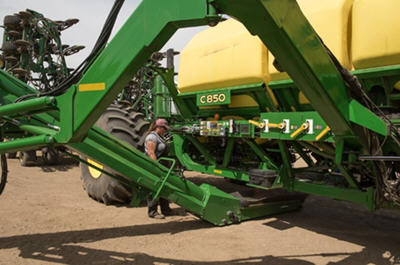
The C850 comes standard with the wireless-controlled hydraulic conveyance system with a low-profile hopper. Maneuvering the conveyor can be done from the wireless conveyor remote or the remote tethered to the cart. With five pivot points on the arm, all tanks can be filled from one spot. The pivot points also allow the conveyor to be easily positioned and moved when filling from a seed tender.
This conveyor moves up to 3524 L (100 bu) of product in a minute with a 40.6-cm (16-in.) belt inside the 30.5-cm (12-in.) tube. By moving the hopper under meter, the conveyor can be used for clean out on each tank as well.
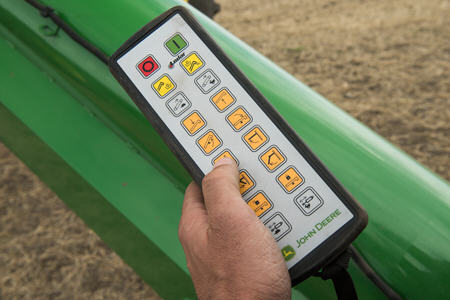
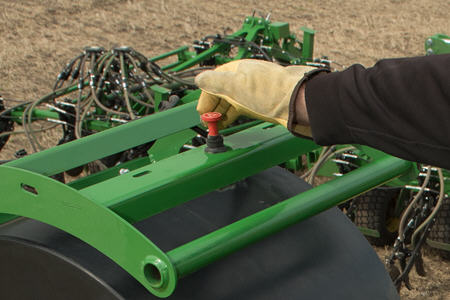
The shut-off switches on the conveyor are located at the bottom of the tube, above the hopper and at the top of the conveyor near the spout. Filling at night is easy with the light-emitting diode (LED) 900-lumen lights on the cart and conveyor conveniently placed to illuminate each meter, the stairway and platform.
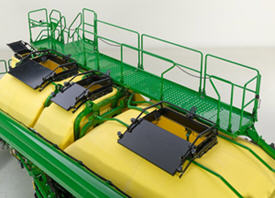
The C850 has five tank lids to make filling convenient and quick. The three back tank lids are operated by pushing forward on the foot pedal and straight down on the handle. The lid slides out of the way, contouring the shape of the tank, so it does not interfere with the conveyor. The tank lids seal tight by pulling upward on the handle and stepping back on the foot pedal. The three back tank lids offer a wide opening, making an easy job out of placing the conveyor in the right place during fills. The design is a single per tank design, providing for faster fill times.
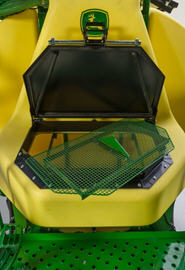
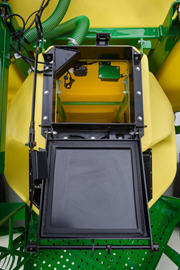
The front 1762-L (50-bu) tank has two options to make loading low rate products easier. If the grower is filling the tank with bags, the front lid is accessible from the lower platform of the cart. The two front railings of the cart can be removed to allow for a truck to bring bags directly to the platform. As pictured above, the bottom fill location of the front tank has a bag splitter.
To fill the front tank with a conveyor, the top tank lid is easily reached with the hydraulic conveyance system.


The stairs to the platform are 33.02 cm (13 in.) from the ground and feature wide, tall, and sturdy handrails that will support operators as they carry bags to the dedicated low-rate, 1762-L (50-bu) tank on the bottom platform. A wheel-speed sensor will automatically fold the stairs as the air seeding train moves. The powered stairs also have a manual release. The stairs are equipped with compression springs to make folding up the stairs manually an effortless task.
The lower platform was designed with comfort and convenience in mind. The front two handrails can be easily removed so operators can load from a skid steer or the back of the pickup truck. The stairs allow access to the mini tank when carrying seed bags. The platform has room designed for seed bag storage with cut outs for tie-down straps in the railing.
To improve scale accuracy, the upper platform has been isolated from the tanks to eliminate interference. With that design, movement of the platform can be expected. The handrail system is foldable so the handrails are flush with the tank lids.
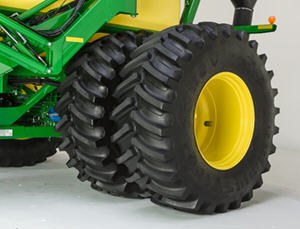

The C850 comes equipped with rear dual Mitas® 800/70R38 SFT tires and front single Mitas 800/70R38 SFT tires as a high-floatation, low-compaction solution. The Mitas tires run at an inflation pressure of 1.3 bar (19 psi). Super flexion tire (SFT) technology means that the sidewalls on the tire are developed with additional reinforcement and superior rubber compounds, which enables the tires to run at a very low pressure while under higher loads without damaging the sidewalls. By running at lower pressure, the tire is able to flex its sidewalls and squat, allowing for a much wider footprint and improving floatation.
An optional tire package for even greater floatation and decreased compaction includes rear dual Firestone® increased flexion (IF) 850/75R42 CFO tires and front single IF 900/75R32 CFO tires. The Firestone package allows for increased air capacity, which provides greater floatation. A proprietary side wall compound and radials allow for a lower tire pressure (0.8ba [12 psi]) which provides lower compaction across a wider footprint.
To see how the tire pressures on the C850 Air Cart compare to the 1910 Commodity Cart, please view the tire pressure guide.
Below is a test conducted by Firestone comparing the impact different size tires have on average flat plate areas and pressures. While it is not an exact comparison to the Mitas tires, which run at a lower pressure than what is used in the study, it gives a general illustration of the additional contact area of the high floatation tires.

Front position comparison | ||
Tire size | 800/700R38 | IF 900/75R32 CFO |
Load | 8913.1 kg (19,650 lb) | 8913.1 kg (19,650 lb) |
Inflation | 1.8 bar (26 psi) | 0.8 bar (12 psi) |
Total area | 5038.7 cm2 (781 sq in.) | 7580.6 cm2 (1175 sq in.) |
Contact area | 1470.3 cm2 (227.9 sq in.) | 1628.4 cm2 (252.4 sq in.) |
Average pressure | 1.7 bar (25.1 psi) | 1.15 bar (16.7 psi) |

Rear position comparison | ||
Tire size | 800/700R38 | IF 850/75R42 CFO |
Load | 7407.2 kg (16,330 lb) | 7407.2 kg (16,330 lb) |
Inflation | 1.65 bar (24 psi) | 0.8 bar (12 psi) |
Total area | 4710 cm2 (730 sq in.) | 7451.6 cm2 (1115 sq in.) |
Contact area | 1362.6 cm2 (211.2 sq in.) | 1950.3 cm2 (302.3 sq in.) |
Average pressure | 1.54 bar (22.4 psi) | 0.97 bar (14.1 psi) |
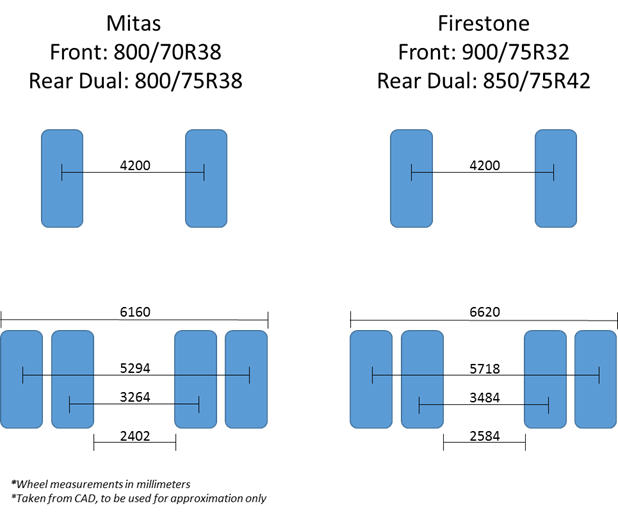
Mitas is a trademark of Mitas, Akciova Spolecnost Corporation. Firestone is a trademark of Bridgestone Americas Tire Operations, LLC.
SectionCommand controls seed and fertilizer overlaps and skips
Controlling input costs and improving productivity are key producer requirements today. SectionCommand is an effective, integrated John Deere solution designed to meet these intensifying needs. SectionCommand manages both seed and fertilizer application by minimizing overlaps and skips while seeding with the John Deere 1910 and C850 Air Carts.
Owner benefits include:
- Improved consistency of crop maturity at harvest
- Improved consistency during emergence and growing season
- Reduced seed input cost
- Reduced fertilizer input cost
- Increased time between fills due to input savings
SectionCommand is base equipment with optional deduct on all John Deere 1910 and C850 Air Carts. Each tank and meter will receive SectionCommand components. A two-tank cart will control sections out of both tanks, a three-tank cart will control sections out of all three tanks, and the C850 cart will control sections out of all four tanks. SectionCommand is also available as an attachment for field conversion (AFC) for all 1910 hydraulic drive carts. See AFC kit story for more information.
SectionCommand controls seed and fertilizer output by closing and opening gates on the bottom side of the meter. When the gates are open, commodity is metered out, and when closed, commodity stays and continues to rotate within the meter. The meter stays full at all times so immediately when the gate opens, the commodity can flow into the primaries and out to the tool. Since each meter section has its own gate, application rates and row-to-row accuracy are not compromised. The gates are utilized to control commodity output on all sections. Once the last gate needs closed, the entire meter will stop turning, stopping product flow.


When commanded, electric over-hydraulic solenoids engage actuators to instantaneously close the gate for the needed section. The actuators are powered via hydraulics from the same circuit as the hydraulic drive motors. When power is cut, oil is diverted to retract the actuators and open the gates. The retraction is both powered and spring assisted, so it will always default to the seeding position. The oil from SectionCommand drains back through the fan motor case drain line and is coupled with an accumulator on the valve block to provide extra drainage capacity.
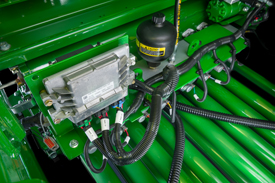
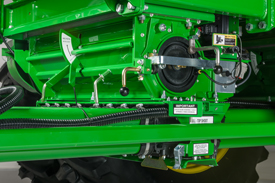
SectionCommand incorporates gate detection, which gives producers the satisfaction of knowing the gates are in position as commanded. Magnets on the back side of the gates are used in close proximity to the gate detection sensors to determine if the gates are open or closed. Should a gate not be in the commanded position, an alarm will alert the operator of the gate(s) in question. The blockage warning system works in conjunction with SectionCommand to give further confidence whether a given section is seeding or not when commanded.
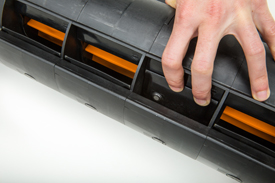
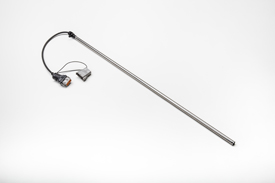
For maximum performance, SectionCommand should be controlled through John Deere Section Control. Coupling SectionCommand with John Deere Section Control provides the ultimate in precision seeding and productivity. If a Section Control activation is held by the producer, that same activation can be utilized for SectionCommand.
SectionCommand introduces the orange roller, which has the same number of flutes and spacing as the blue roller, but shorter flutes. It is for use only with SectionCommand when seeding seeds larger than 6 mm (0.25 in.) in diameter (soybeans, chick peas, etc.). The orange roller is not for use with cereal grains or fertilizer.
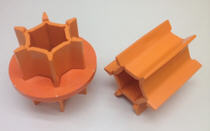
SectionCommand equalizer
Due to the varying lengths of product delivery hose used across the drill, SectionCommand has a built in equalizer feature to ensure consistent product delivery across the width of the drill when entering and exiting headlands. The software allows the producer to set the on/off product delivery times separately for the outermost opener and the innermost opener on the drill. Product delivery times are inputted for each tank on the cart, and the software creates a time delay for actuation of the gates.
Please see the Using SectionCommand video for more information.
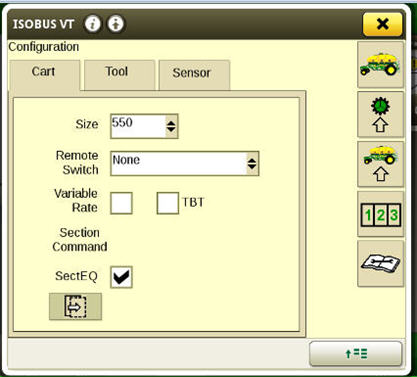
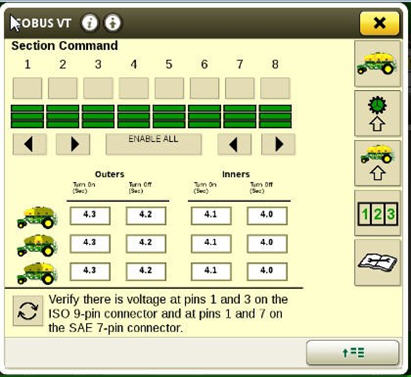
NOTE: Please reference CCMS solution 111434 for more information.
A meter cartridge at each tank effectively meters seed or fertilizer into the primary manifold. Air carries the material to the secondary distributor for delivery to the openers on the seeding tool.
Meters are contained in a cartridge for convenient removal and are color coded for easy identification.
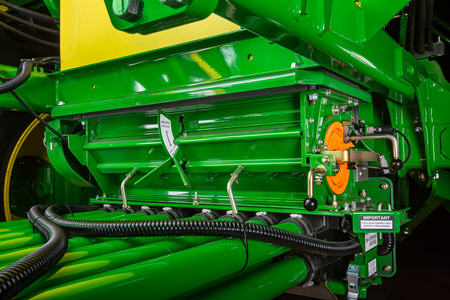
A manual half-width disconnect is incorporated into the 1910 meter system:
- Allows one-half of the metering system to be manually shut off for irregular shaped headlands, point rows, etc. on mechanical drive carts.
- Allows the meter cartridge to be removed with material still in the tank(s).
- Allows tanks to be emptied with meter and primary manifold in place.
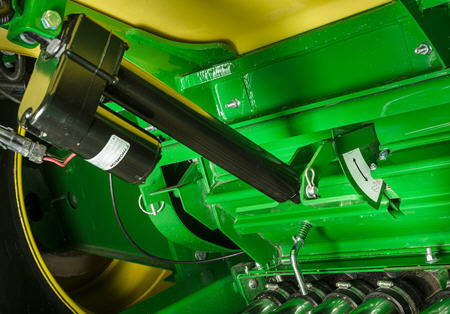
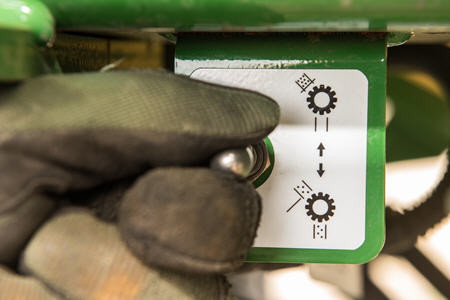
On the C850 Air Cart an electric actuator controls product flow from the tank to the meter housing:
- Allows complete shut off of product flow with little effort
- Allows the meter cartridge to be removed with material still in the tank(s).
- Allows tanks to be emptied with meter and primary manifold in place.
Specifications
Key Specs | c850-air-cart Current Model |
---|---|
First tank capacity | 1762 L 50 bu |
Second tank capacity | 9162 L 260 bu |
Third tank capacity | 4581 L 130 bu |
Fourth tank capacity | 14448 L 410 bu |
Drive type | Hydraulic |
Maximum rpm | 249.5 kg (550 lb) of seed per acre at 8.9 km/h (5.5 mph) and 15 degree slope (136.1 kg [300 lb] of fertilizer and 113.4 kg [250 lb] of seed) |
Minimum transport width | 6.62 m 21.67 ft |
Minimum transport height | 4.03 m 13.25 ft |
Minimum transport length | 14.6 m 48 ft |
Weight empty | 18552 kg 40900 lb |
Capacity | |
Configuration | |
Tow between | |
Tow behind | Tow-behind only |
Tanks | |
Type | |
Quantity | 4 |
First tank capacity | 1762 L 50 bu |
Second tank capacity | 9162 L 260 bu |
Third tank capacity | 4581 L 130 bu |
Fourth tank capacity | 14448 L 410 bu |
Lid size | |
Liquid capable | |
Liquid capacity | |
Open lid indicators | |
Auger | |
Standard | |
Optional | |
Meters | |
Drive type | Hydraulic |
Metering system | |
Settings | |
Rates | |
Power calibration (hydraulic) | |
Meter shutoffs | |
Monitoring | |
Standard | |
Optional | |
Fan speed | |
Ground speed | |
Meter speed | |
Bin levels | |
Area covered | |
Rate change | |
Main clutch engagement | |
Tank meter clutch engagement | |
Documentation available | |
Map-based prescriptions available | |
Fan | |
Drive | Hydraulic |
Maximum rpm | 249.5 kg (550 lb) of seed per acre at 8.9 km/h (5.5 mph) and 15 degree slope (136.1 kg [300 lb] of fertilizer and 113.4 kg [250 lb] of seed) |
Hydraulic flow, maximum | |
Standard quantity | |
Optional quantity | |
Diameter | 69.85 cm 27.5 in. |
Speed range | |
Drives | |
Type | |
Variable-rate drive | |
Variable-rate control | |
Front tires | |
Rear tires | |
Dimensions | |
Minimum transport width | 6.62 m 21.67 ft |
Maximum transport width | |
Minimum transport height | 4.03 m 13.25 ft |
Maximum transport height | |
Minimum transport length | 14.6 m 48 ft |
Maximum transport length | |
Weight empty | 18552 kg 40900 lb |
Accessories and Attachments
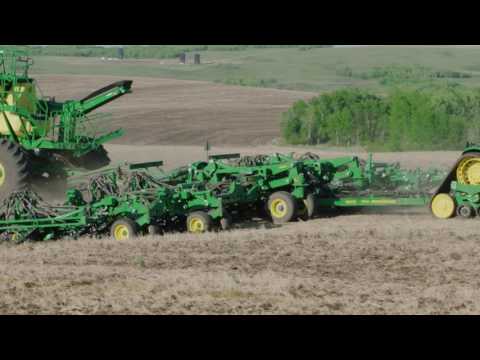
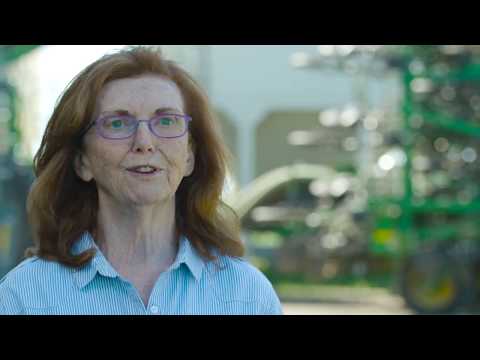
© 2024 Valley Plains Equipment LLC - Powered By